This is a big feature in my car factory game Production Line that I have been putting off until I could really set aside some time to think about the design seriously. I think I’ve finally reached that point in Early Access where I need to flesh out the design for this part of the game, and also importantly, to listen to feedback from current PL players about how they think this should work.
The current system is pretty simple. cars have work done to them on the production line, and then at the very end of the line, just before export, they go through a pre-export QA process that is broken down into emissions test, visual inspection and performance tests. All cars are assumed to be thoroughly free of defects, and are sold on the basis of their features and their price relative to the perceived value of those features.
Obviously in the real world, defects and car quality is a thing. You wouldn’t expect any defects on a $150,000 car, you would expect very few on a $70,000 car (unless its panel gaps on a tesla…dig dig…), and probably be more tolerant of minor things on a cheaper car. High end car companies (Rolls Royce etc) probably go overboard on quality assurance to ensure a reputation for zero problems (Lexus are also good at this), whereas at the lower end, its probably less of a concern. How to best represent this in the game in a way that both feels reasonable, and makes intuitive sense, and also works within the existing game design, and above all feels interesting and fun?
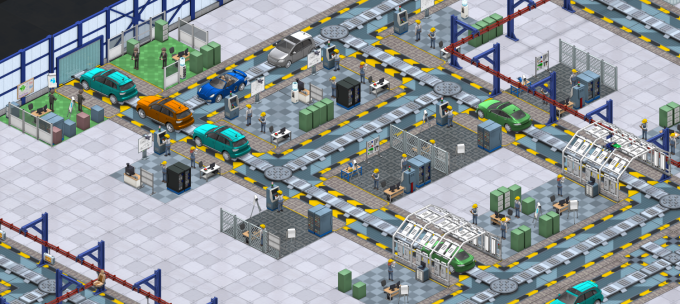
For a while, I have wanted to combine the idea of defects with the introduction of an area-of effect mechanic. One of the most interesting aspects of the game is the designing the layout of your factory, and at the moment, apart from making sure importers and exporters are in the right place, and ensuring that you only place office slots (like research) in office zones, there is not that much *positional* decision making involved in the game. I thought I could introduce this with the advent of new QA slots, that had a radius effect.
The system would work by generating defects at every point along the line. there would be a base level of defects that would be generated each time a task was carried out on a vehicle, including tasks generated through upgraded slots. For example, adding the rear axle = 1% chance of a defect. Adding a tire pressure sensor… 1% chance of a defect… and so on. Some cars would go through the line entirely free of defects, but many would not. Eventually, if ‘untreated’, those defects would make their way into the final cars which would be sold.
For every car sold with defects (depending how many), there would be a negative impact on the reputation of your brand, a new, lagging indicator which would affect the purchase enthusiasm of your customers. Obviously this would be something you would want to keep an eye on, so as to ensure customers were not turned away, so how do you prevent defects? and how do you treat them?
To prevent defects, you can place down QA stations, which would be area-of-effect based, and would essentially reduce the percentage chance of a defect occurring at any specific point on the line. Covering the entire production line with regular QA slots would be a way to keep production quality high and defects low, but obviously would have a cost in terms of employee pay and the floor-space required to add those QA stations. This would be a ‘prevent defects from ever happening’ approach to QA. The second approach would be to introduce a new ‘re-work’ slot right at the very end of the line (maybe just before the current QA section) which would examine each car, and take whatever time is needed (maybe 2 minutes per defect?) to fix the problem and allow a perfect car to travel beyond that point. Clever players would eventually use smart junctions (which would need defect-based rules added to them) to ensure that cars that randomly seemed to be defect-heavy did not cause a major slowdown. As I understand it, in real factories, cars that need re-work are immediately taken off the line and dealt with separately so as not to cause any real bottleneck.
This is my first attempt at designing a QA/Quality system for the game. I’m very interested to know what existing (or potential) players of the game think. Essentially it boils down to this:
- Defects are randomly generated on cars as they are constructed
- Area-of-effect QA stations reduce the likelihood of those defects when placed on the line
- A re-work area can optionally be placed to fix defects at the end of the line
- Defects will affect the brand image of the company, and thus customer eagerness to buy.
Thoughts?